Powder & Bulk Solids is part of the Informa Markets Division of Informa PLC
This site is operated by a business or businesses owned by Informa PLC and all copyright resides with them. Informa PLC's registered office is 5 Howick Place, London SW1P 1WG. Registered in England and Wales. Number 8860726. Pellet Granulator Machine
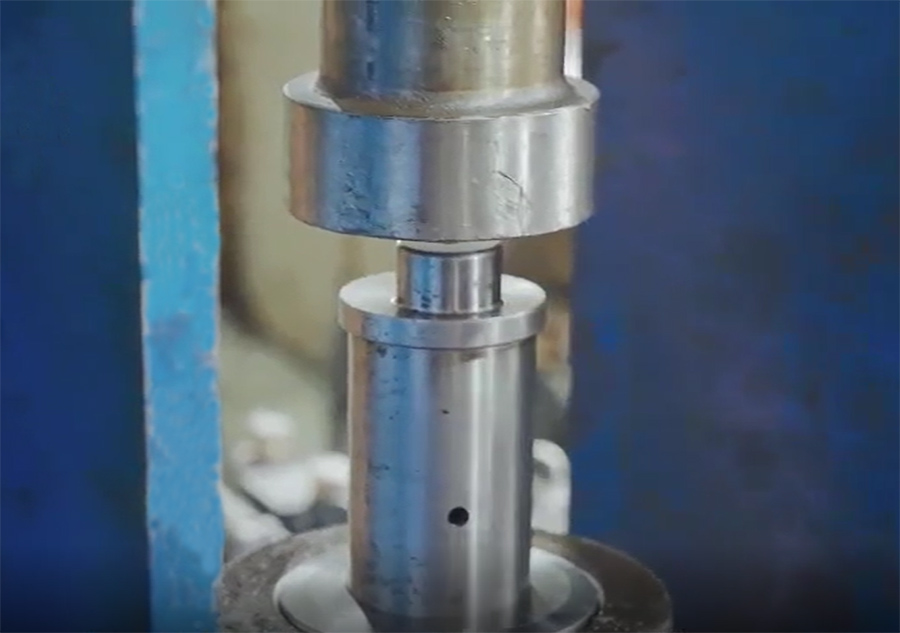
See All Safety & Compliance »
Brandon Dohn, global industry applications manager, Coperion K-Tron | Jul 21, 2023
An extremely popular method for transporting large quantities of bulk solids is pneumatic conveying. This should be no surprise as it has numerous benefits over various mechanical counterparts including enclosed pipework, low maintenance, minimal moving parts, and the ability for potential systems to traverse complex isometric (pipe) routings especially where distances are excessive. Passing regulatory compliance hurdles associated with certain hazards or industries can be less cumbersome with pneumatic conveying systems.
On occasion, the debate brews for solids handling professionals and end users alike, “dilute phase conveying or dense phase conveying?” While the answer is never simple the conclusion is often drawn before considering several factors that will have a lasting impact on your plant operations for years to come. This article will briefly define the difference between the two modes, the often-cited reasons for choosing dense phase, and the potential pitfalls that often go unnoticed producing the very outcome processors set out to eliminate in the beginning: poor performance and high cost of ownership.
Let us begin by defining the traditional modes of pneumatic conveying. Dilute phase conveying, also referred to as lean phase, is a method of solids transport where particles are in complete suspension by the transport gas as they are blown or vacuumed through an enclosed pipeline (Mills, PCDG, 2nd addition). To produce this mode of conveying there must be sufficient gas velocity, usually in excess of 20 m/s. One unique benefit of this conveying mode is that almost any bulk material can be transported reliably using this method. When comparing this conveying phase to its complement the single largest drawback is the velocity required to generate stable conveying. Dilute phase conveying can require large volumes of air by comparison, and henceforth large quantities of air can have a proportionally direct impact on the power required. Further, velocities generally have a mathematically square impact on the convey line erosion and abrasion (Klinzing 1989).
Dense phase conveying is often defined as the inverse of dilute phase conveying. That is to say that the particles conveyed in the pipeline are not suspended completely in the gas and the flow mode can be recognized either as a moving bed or in single pistons, equivalent in diameter to the convey line with gas voids between each slug. This mode is achieved using a smaller quantity of convey gas and ultimately lower line velocity resulting in reduced wear on pipelines and components. Invariably generating smaller quantities of conveying gas can also lead to a reduction in energy usage and maintain the integrity of the product being transported. Dense phase conveying is often promoted for use on material blends and mixtures to minimize a phenomenon known as segregation which is the de-mixing of bulk mixtures.
Upon initial glance at the two definitions, one might succumb to the verdict that dense phase conveying is clearly the superior method for transporting bulk materials in a pipeline. While this is certainly true for some materials and processes there are many overlooked factors when drawing this conclusion.
Moving forward in this article are points to consider before choosing the best method of conveying your products and process.
Consider again that the very parameter that distinguishes dilute phase conveying from dense phase conveying, and vice versa, is velocity. Researching the topic further using common search engines or speaking to manufacturers of the technology will yield terminology differentiating the two modes using “solids loading ratio” and “high pressure vs. low pressure.” While it is true that such characteristics can be used to diagnose the mode of conveying these attributes are only symptoms. Many dilute phase conveying systems operate at pressure differentials well above 1 bar(g) [15 psig], which is the often-sought benchmark to distinguish dilute phase from dense phase. The opposite circumstance can also take place in the real world. Thankfully there is a demonstrative that tells the story of pneumatic conveying perfectly shown in Figure 1.
Image courtesy of Coperion K-Tron Figure 1: Modes of pneumatic conveying
Figure 1: Modes of pneumatic conveying
As shown in Figure 2, a phase diagram for a pneumatic conveying system is quite simple to interpret. The “y-axis” is representative of the pressure drop of a conveying system, and the “x-axis” constitutes the change in velocity. The various intermediate lines on the diagram are the throughput of bulk material in their respective pneumatic conveying regime. Put simply, with capacity held constant, if the material velocity starts on the right side of the diagram (the dilute region) and transitions to the left the material will fall from suspension and begin conveying in a dense phase mode.
Again, the only manipulated parameter was the velocity, and to achieve the required capacity in the identical system, the convey gas pressure must increase. Depending upon the capacity in question the pressure differential could be significantly higher when comparing that same capacity in the dilute phase conveying region. As a result, processors will have to consider componentry for the system that is rated to handle the anticipated higher pressures including air compressors, differing sources such as pressure vessels or high-pressure rotary valves, diverter valves and piping connections. Most of these items are available for such processes, however at higher expenditure costs that should be considered.
To follow the commentary on system componentry it is worth mentioning that dilute and dense phase systems will utilize the same general building blocks: a motive air source, a feeding device, an enclosed pipe, and a destination bin. Their typical installation guidelines vary, however.
An example is to consider the destination bin. Often the bin receiving the solids will have a filtration device (i.e., bin vent or other filter device) that separates the particulates from the air. As time progresses the filters will diminish in life, and devices such as differential pressure monitors can help processors assess the life expectancy of their filter media. With dense phase systems often operating at much lower air volumes, by comparison such devices may not be reliable in trending the maintenance cycle of such devices.
Special considerations are especially important for operator and personnel safety. Since the dense phase conveying systems can often exceed operational pressures above 1 bar(g) [15 psig] much of the equipment will fall under the design purview of the American Society of Mechanical Engineer’s (ASME) Codes & Standards. A processor must not only consider the elevated nature of LOTO procedures for high pressure devices, but also the additional time and expenditures associated with distinct (high pressure) pipe connections and inspections prior to commissioning the system.
Irrespective of the conveying mode there are generally a unique set of instructions for installing the system. Reputable and experienced systems suppliers will have their own published set of guidelines addressing common items associated with conveying systems.
One of the most overlooked aspects of any pneumatic conveying system is the potential isometric routing of both the clean air and convey lines. Common requirements on dilute phase pneumatic conveying systems are to keep all lines in the horizontal and vertical plane, include acceleration zones for the material and avoid consecutive elbows. This advice may not necessarily apply to dense phase systems.
For dense phase systems that transport certain materials, it may be recommended that an elbow immediately follow the pickup point and traverse vertically to assist in the formation of slugs. This rule is contrary to typical pneumatic conveying systems and is often met with enthusiasm given the ease it creates during the design process. Further, elbows in dense phase systems may not need to be traditional radius bends for more common conveying systems easing potential design constraints further.
Pipe forces are generated in dense phase systems, and this phenomenon is one most processors fail to observe during the design phase. In some instances, suppliers neglect to consider it leading to potentially damaging consequences including injured operators and material breaches from the convey line. Such forces are common in convey routings with large diameter lines (>100mm), excessive elbows and excessive horizontal sections of pipe. Since slugs of material can often have equivalent lengths in excess of 20 times the pipe diameter and travel at speeds between 6 to 10 m/s processors must consider structural reinforcements where the pipe and elbows will be routed. Uniquely designed pipe support may also be required to help distribute radial and axial movements along the pipework when material impacts directional changes. Processors should work with suppliers that have experience and established methods to calculate and design for these circumstances.
Ideally, materials that are suitable for dense phase are granular in particle size, have a Carr Index number of
Thankfully there is another guideline that can assist processors in qualifying their material as suitable: The Geldart Classification Chart (see Figure 3). In summary, this chart draws a relationship between a solid’s bulk density and its respective particle size distribution to determine the fluidization behavior of the solid in question. The explanation of the ideal candidate above would lie in the ‘D’ region of the chart (see article). Group ‘C’ materials can often be excluded from consideration in dense phase due to their cohesive nature. Examples include titanium dioxide, certain PVC compounds and ascorbic acids. Group ‘A’ and ‘B’ materials can often be considered suitable given the potential for aeration and fluidization. In dense phase systems if materials do not form slugs naturally the alternating state of flow is dense phase fluidized. Maintaining this state in the convey line can prove difficult as most bulk solids do not react well to staying fluidized while simultaneously being compressed from a motive air source. To remedy this, most processors will elect to employ “boosters” or “stabilizers” along the pipe routing to keep the material aerated and stable by bleeding in small amounts of air. Such devices are useful, however, the energy saving benefits of dense phase systems are often nulled by employing them. Additional concerns should arise for processors of RTE foods and APIs attempting to use such devices as compressed air quality standards will need to be recognized. The air assist devices will also need to occupy the pipe interior and processors should take special care to ensure crevices are minimized or eliminated.
Image courtesy of HATCH Geldart material classification chart
Charts and equations are useful in determining a material’s suitability to remain stable during dense phase transport, but there is no substitute for full scale material trials. Prospective buyers should consult with vendors on their testing capability and know how to eliminate any doubt.
Processors that blend bulk materials often select dense phase conveying when transport of the material is required. The logic is sound – if dilute phase is high velocity by definition the product will likely de-mix or segregate during transport. This is true, but not exclusive to dilute phase systems.
Dense phase systems that largely ignore the considerations above can also subject blends to segregation. This is especially true when the dense phase system in question utilizes air assists along the convey line. Injecting air along the convey line will influence the upper portion of the material to differ in transport speed when comparing the bed in contact with the pipe – which is also experiencing drag forces.
If the particle size distribution of the blend varies greatly neither dilute phase or dense phase may be suitable as the larger particle inertia will vary disproportionately to the smaller, lighter particles. The problems most often associated with blend segregation as a function of pneumatic conveying are those which consider the system design in totality including length of vertical runs, horizontal runs, and number of bends. Material entry into a bin (tangential vs. radial) will also play a role. The best practice to minimize blend segregation in pneumatic conveying is to avoid numerous handling steps after the mixer, design the convey routing to be as simple as possible, and target a velocity that transports all particles in a similar proportion.
Dense phase conveying has enumerated benefits for many processors, and similarly to any value-added technology, those benefits arrive at a cost. Until recently many designers of dilute phase systems considered the “worst case” design scenarios of longest distance and highest capacity when proposing conveying systems. Couple that with fixed speed motive air sources and single speed feeding devices and the result is unnecessary wear, product inconsistency and increased energy usage. With the cost of variable frequency drives continuing to decrease by comparison to their across-the-line compliments, along with the inception of PLC-based algorithms to cater air volume in cadence with pressure differential there are potentially new, cost-effective ways to achieve the goals required by the material handling process. As you progress in your journey to design the proper material handling system, I hope this article helps consider the best method of conveying your products and process.
Brandon Dohn is global industry applications manager, Coperion K-Tron (Salina, KS). For more information, call 785-825-1611 or visit www.coperion.com/en.
More information about text formats
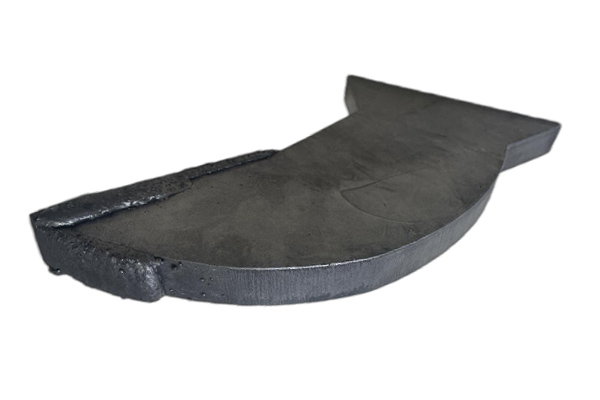
Pneumatic Vacuum Conveyor Check out Powder & Bulk Solids Industry Master directory.